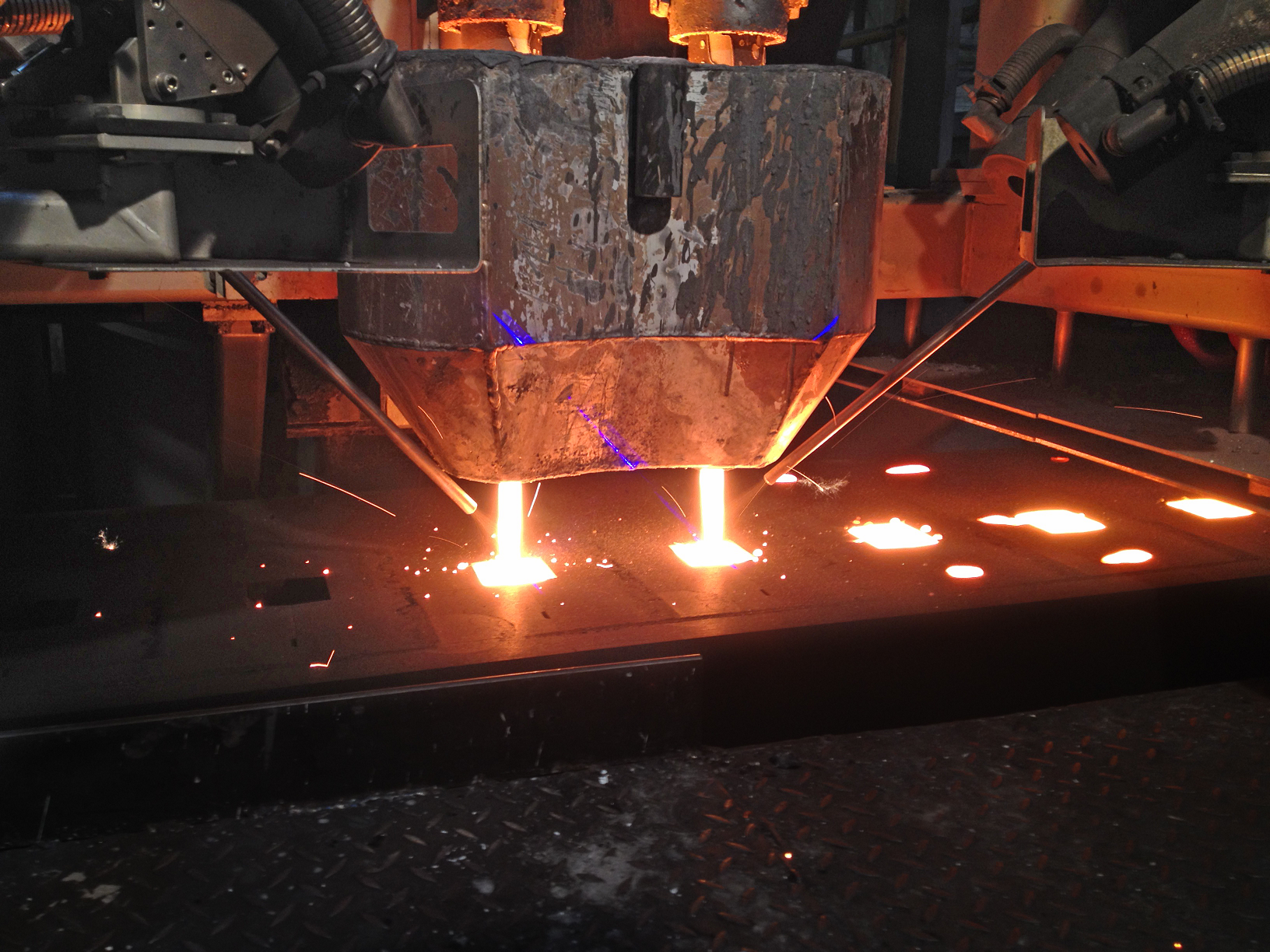
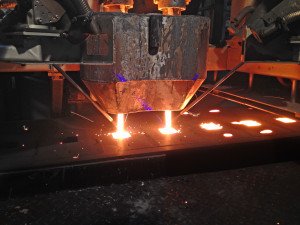
AI Operator for Iron Foundries
Pour-tech AB, a company specialized in automatic pouring systems for iron foundries, wanted to upgrade their pouring technology to an intelligent automated system that did not require human intervention from operators. In this use case, it is discussed how machine learning algorithms and PLC simulation data were used to automate the metal pouring operation.
Pour-tech AB aspired to upgrade their current pouring technology from a PID-based system, which required intervention from an experienced operator.
The goal was an intelligent automated pouring system that required no intervention from the human operator, that fulfilled the following criteria:
- End-to-end automated pouring solution based on data-driven model predictive control systems.
- Scalable and deployable in real-time for continuous pouring including multiple types of molds in foundries around the world.
Based on process and production data, Viking Analytics developed machine learning algorithms that, once deployed, evaluate information from each pour and adjusts the parameters for the next one.
In practice, it means that the system is always improving itself, by learning from past actions in a feedback loop that maintains long-term quality. And it happens in a fraction of time that it would take for an operator to make the same decisions.
A Proof-Of-Concept (PoC) was developed in 4 months and the scaled up industrial solution was deployed & tested in another 4 months.
It eliminates overpours and scrap, resulting in significant reductions in re-melt costs. It also provides stability in product quality and higher productivity. At the foundry where the system was first implemented, gains of 0.10€ per pour have been registered.
Currently, two foundries in Denmark and Germany are already successfully using the AI Operator.