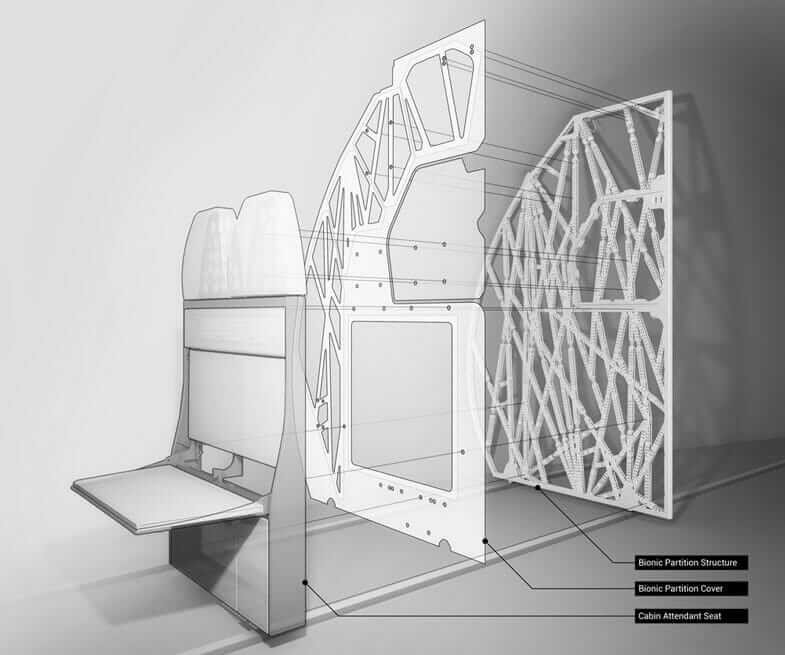
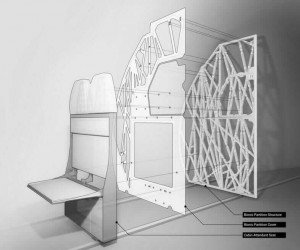
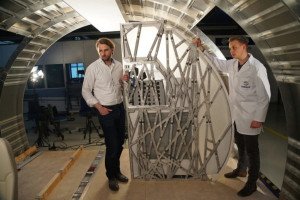
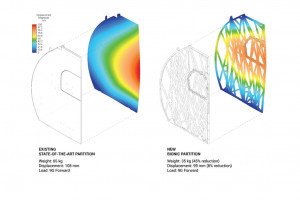
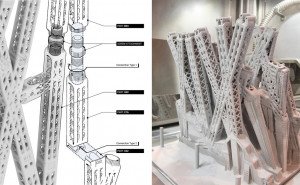
Airbus Partition Wall Generative Design
Bastian Schaefer is the aptly titled Innovation Manager at Airbus, the aircraft manufacturer, in Hamburg, Germany. His mission: Find new ways to make jetliners more efficient and comfortable.
For some passengers, “comfortable” means the freedom to use technology to work, play, and collaborate. For others, it’s greater accessibility, more privacy, or just more room. “Our challenge is to address all of these things in a flexible, dynamic way,” he says.
As part of the team that developed the Airbus Concept Plane—a vision of the jetliner of 2050—Schaefer’s insights are shaping how passengers will travel in the future. For example, they’ll be offered customized flight experiences based on their desired activities. Flights will also be more eco-friendly. The plane of the future will be designed to be much lighter, to use less fuel, and to leave a smaller carbon footprint. “Light is good, but we can’t lose strength or safety,” Schaefer says.
This complex vision relies on a cutting-edge technology inspired by nature: generative design.
After introducing the Concept Plane, the team members began to explore components that would use the new technologies they’d proposed. They chose an unassuming but key piece of the aircraft: the partition that separates the passenger compartment from the galley in the Airbus A320 cabin.
This new partition had to:
- be significantly lighter than the current partition, to meet the goal of reducing the weight of the plane,
- be strong enough to anchor two jump seats for flight attendants during take-offs and landings,
- have a cutout to pass wide items in and out of the cabin,
- be no more than an inch thick, and
- be attached to the plane’s airframe in just four places.
Meeting these design constraints required a major departure from traditional engineering approaches. Schaefer began working with Autodesk Research, using generative design to develop what the team called “the bionic partition.”
Generative design is a technology that mimics nature’s evolutionary approach to design. It starts with your design goals and then explores all of the possible permutations of a solution to find the best option. Using cloud computing, generative design software quickly cycles through thousands—or even millions—of design choices, testing configurations and learning from each iteration what works and what doesn’t. The process lets designers generate brand new options, beyond what a human alone could create, to arrive at the most effective design.
Airbus’s bionic partition needed to meet strict parameters for weight, stress, and displacement in the event of a crash with the force of 16g. To find the best way to meet these design requirements and optimize the structural skeleton, the team programmed the generative design software with algorithms based on two growth patterns found in nature: slime mold and mammal bones.
The resulting design is a latticed structure that looks random, but is optimized to be strong and light, and to use the least amount of material to build.
3,180 KG OF FUEL SAVED PER PARTITION,
PER YEAR
The bionic partition may be a relatively small part of the plane, but installing this lighter component could help airlines begin to make a positive difference for the environment. For each 1 kilogram (2.2 pound) reduction in weight, jet fuel use is cut by 106 kg (233.2 lb) a year, helping to decrease the carbon footprint of air travel. Each partition is approximately 30 kg (66 lb) lighter than the standard partition.
166 METRIC TONS OF CO2 EMISSIONS CUT PER YEAR, PER PLANE, FOR AN AIRBUS A320 INSTALLED WITH BIONIC PARTITIONS
If bionic partitions are installed throughout the entire cabin of an Airbus A320—four per plane—that would remove up to 500 kg (1,102 lb) of weight. The resulting decrease in fuel use would cut CO2 emissions by up to 166 metric tons per aircraft each year. Multiply that by the thousands of new A320s on order, and airlines have the potential to reduce CO2 emissions by hundreds of thousands of metric tons per year.
95% LESS RAW MATERIAL
In addition, 3D printing will help reduce the company’s environmental impact. The process uses only 5% of the raw material that the traditional process of milling parts down from a metal block uses. And with 3D printing, whatever raw materials are left over can be reused to manufacture another part.